March 11th, 2025
Category: Manufacturing
No Comments
Posted by: Team TA
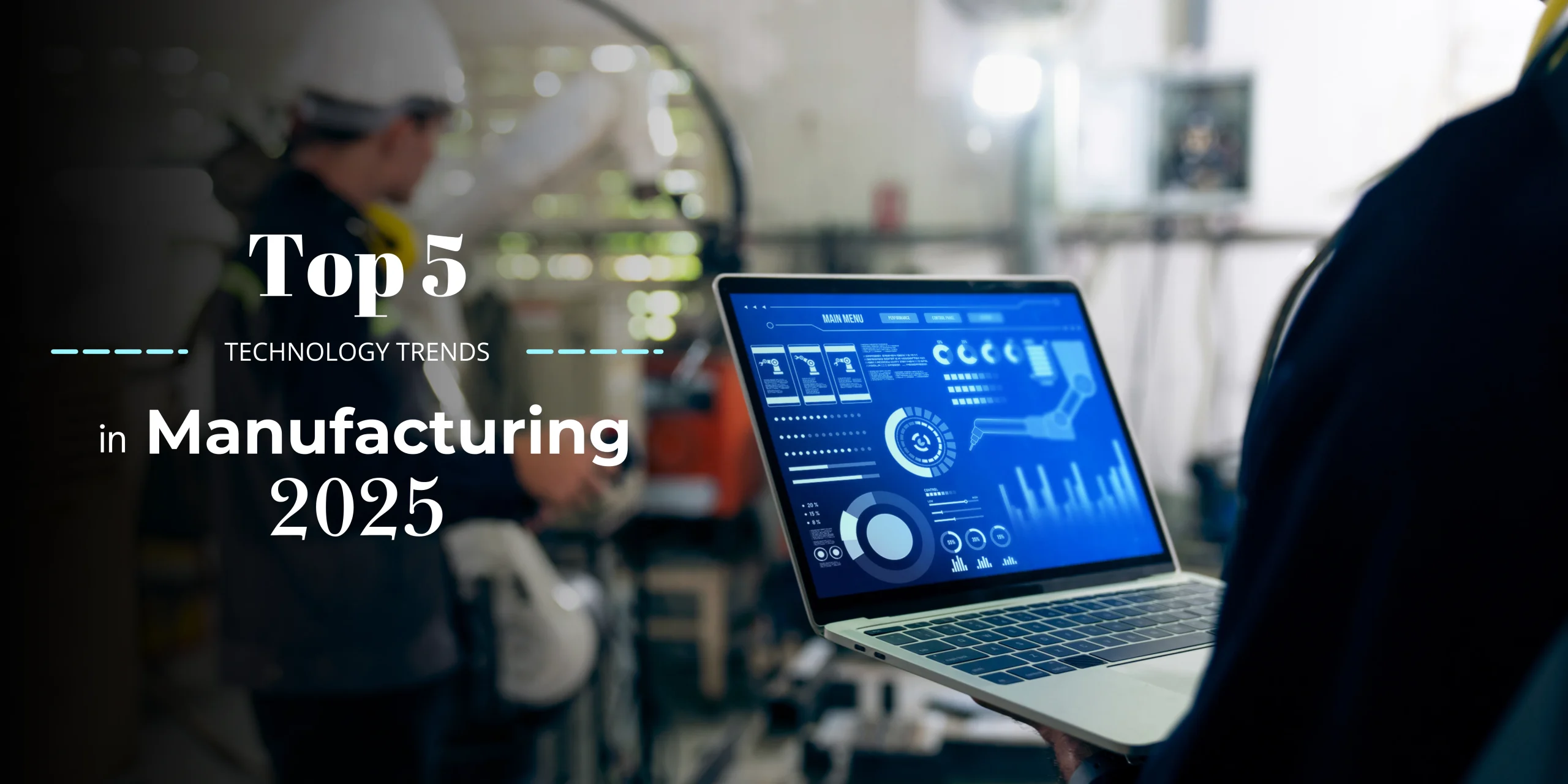
The manufacturing industry is undergoing a rapid transformation, fuelled by technological advancements. Specifically, integrating advanced analytics, sophisticated robotics, and the Industrial Internet of Things (IIoT) is reshaping production processes. Recent McKinsey research states that digital transformation in manufacturing can decrease machine downtime by an impressive 50%, improve quality costs by 10–20%, and increase productivity by 10–30%. Furthermore, a Deloitte study shows that businesses with higher levels of digital maturity saw faster growth in revenue and profit. To maintain a competitive edge and optimize operational efficiency, manufacturers must proactively adopt these technological trends. This blog post explores 5 recent trends in the manufacturing technology industry in 2025 and beyond.
1. Smart Factories – Leveraging IoT & Automation
Smart factories, a key aspect of Industry 4.0, are improving manufacturing processes. By 2032, the smart manufacturing market is projected to grow from $223.6 billion to $985.5 billion, according to Precedence Research. This approach improves efficiency across the manufacturing lifecycle by utilizing technologies like automation, artificial intelligence, and the Internet of Things (IoT). Smart factories provide integrated environments where machines and humans connect fluidly, revamping processes from supply chain management to quality control.
What Makes IoT Essential for Smart Factory Success?
IoT collects real-time data from equipment and production processes through sensors, enabling predictive maintenance, efficient inventory management, and improved quality control. For instance, sensors in collaborative robots (cobots) and autonomous mobile robots (AMRs) help detect nearby obstacles, improving safety. Companies like Toyota use IoT to optimize machine maintenance, reducing downtime and increasing overall production efficiency.
Automation in Smart Factories
Automation uses technology to complete tasks without human help. In smart factories, automation systems control machines, conveyors, and robots for repetitive or dangerous jobs. According to Forbes, currently, 32% of production lines use both robots and collaborative robots (cobots), which work alongside humans. Equipped with advanced sensors for safety, cobots handle tasks like assembly and quality inspection. Additionally, automated guided vehicles (AGVs) and autonomous mobile robots (AMRs) improve material handling and logistics, boosting efficiency.
Smart Factories Today
✔ Bosch’s smart factory uses digital twins and robotics, connecting over 60,000 sensors with Nexeed software to enhance production efficiency by 25% and cut component costs by up to 50%.
✔ General Electric’s Brilliant Factory employs the Predix platform and Industrial IoT sensors for real-time analytics and predictive maintenance, optimizing operations continuously.
Why Smart Factories Are the Key to Next-Gen Manufacturing Success?
For decision-makers in the manufacturing sector, smart factories are no longer a futuristic concept—they are a necessity for staying competitive. By leveraging IoT, automation, and AI-driven insights, businesses can reduce operational costs, enhance productivity, and improve quality control.
Adopting smart factory solutions means more than just efficiency gains; it opens the door to predictive maintenance, real-time decision-making, and a more agile supply chain. Companies that invest in these technologies today will be better positioned to meet rising customer demands, adapt to market shifts, and drive long-term growth.
Are you ready to transform your manufacturing processes?
2. AI Integration to Enhance Quality Control and Maintenance
Through demand forecasting, supply chain optimization, quality control, and predictive maintenance, artificial intelligence (AI) applications in manufacturing significantly improve operations. Technologies like machine learning, computer vision, and natural language processing analyze large data from sensors and production lines, which maximize quality and efficiency while decreasing downtime. Computer vision identifies flaws in photos and videos more quickly than humans, outperforming humans in spotting irregularities.
AI in manufacturing boosts the quality control through:
Real-time Defect Detection:
Continuous monitoring using sensors and AI models identifies and resolves issues instantly, reducing downtime and preventing faulty products.
Improved Precision:
AI algorithms analyze vast data, outperforming humans in identifying even the smallest defects, guaranteeing constant quality and quick checks.
Predictive Maintenance:
AI can foresee when equipment will break down, allowing for preventive maintenance, increasing the lifespan of machines
Resource Optimization:
Automation decreases operating costs, avoids material waste through early detection, and eliminates manual work, all of which increase efficiency and profitability.
AI in Manufacturing: Real-world Examples
✔ Siemens
Siemens integrates AI-powered computer vision in quality control to accurately identify defects. Real-time analysis of images and videos finds flaws like dents and misalignments, reducing defective items. AI works continually to increase productivity and identify patterns to prevent future mistakes.
✔ Foxconn
Foxconn enhances quality control with AI and computer vision, ensuring high standards in electronics manufacturing. AI analyzes images to detect faults, while machine learning predicts potential defects using real-time sensor data, enabling proactive quality assurance.
How AI Reduces Downtime and Enhances Product Quality in Manufacturing?
For manufacturing leaders, integrating AI into quality control and maintenance is no longer optional—it’s a strategic advantage. AI-driven defect detection, predictive maintenance, and resource optimization can significantly reduce production errors, lower operational costs, and extend equipment lifespan.
By adopting AI-powered solutions, manufacturers can ensure consistent product quality, minimize downtime, and enhance overall efficiency. Companies that leverage AI today will be better positioned to meet growing industry demands, stay competitive, and drive long-term profitability.
Is your factory ready to embrace AI for smarter manufacturing?
3. Immersive Tech for Transforming Training and Remote Operations
Extended Reality (XR), including VR (Virtual Reality), AR (Augmented Reality), and MR (Mixed Reality), is transforming manufacturing industry by enhancing training, safety, and efficiency. Employees can practice challenging tasks in a safe environment using virtual training solutions, which lower expenses and downtime, particularly in additive manufacturing. Human workers can make better decisions using AI and XR, assuring flexibility in a rapidly changing industry while bridging skill gaps and improving workforce readiness.
✔ Enhancing Workplace Safety
In manufacturing, safety is critical, yet conventional training approaches frequently fall short. When learning new equipment, workers—even seasoned ones—face dangers. By offering detailed instructions and minimizing errors, immersive technologies such as virtual reality and augmented reality enable safe training in a controlled environment.
✔ Addressing Skill Gaps
A recent report from The Manufacturer shows that 97% of manufacturers find hiring and keeping skilled workers difficult, with 75% citing this as their biggest barrier to growth. Immersive technologies, such as virtual reality (VR), provide safe and efficient training to solve this issue, enabling people to acquire skills quickly and confidently without the risks associated with actual manufacturing or machinery. By familiarizing employees with the operating environment, AR and VR simulations facilitate confidence-building. As a result, they provide practice without the danger of consequences in the real world.
✔ Reducing Training Costs and Downtime
Traditional training in manufacturing can be costly due to expenses and lost productivity. Shutdowns for training affect output. Workers may learn in virtual settings thanks to affordable solutions like augmented reality and digital twins. These solutions minimize downtime and wear on equipment, thus saving money and preserving productivity.
Why Manufacturing Leaders Are Investing in Immersive Tech for Workforce Development
Adopting immersive technologies like VR, AR, and MR isn’t just about innovation—it’s a strategic move to enhance workforce readiness, improve safety, and reduce operational costs. By integrating XR solutions, companies can accelerate employee training, bridge skill gaps, and minimize workplace risks, all while maintaining productivity.
With the ongoing skilled labor shortage in manufacturing, immersive technologies provide a scalable and cost-effective way to train employees efficiently. Additionally, AR-powered remote assistance can reduce machine downtime and optimize troubleshooting, keeping operations running smoothly.
Investing in XR today means future-proofing your workforce and ensuring your organization stays competitive in an evolving industry.
Are you ready to embrace the next generation of industrial training and remote operations?
4. Digital Twins and Predictive Maintenance
A digital twin is a virtual model of a physical object or system that shows its lifecycle. It uses data from the past, present, and future to help improve efficiency and product development. In manufacturing, it allows monitoring and optimizing processes without physical trials or field visits.
A digital twin provides real-time data, analytics, and simulations to predict equipment failures, reducing costly downtimes and effectively extending asset lifecycles.
The following are some ways in which Digital Twins improve predictive maintenance:
✔ Real-Time Monitoring and Analysis
A digital twin enhances real-time monitoring in manufacturing by analyzing data from sensors on equipment. This proactive approach enables the early detection of anomalies, allowing for timely maintenance actions that minimize downtime and optimize performance.
✔ Predictive Analytics and Failure Forecasting
Digital twin technology allows manufacturers to access predictive analytics by evaluating both past and present data. This innovative approach enables accurate forecasting of equipment failures, allowing a shift from reactive to proactive maintenance strategies. As a result, resources can be optimized, downtime can be reduced, and maintenance efforts can be focused where they are most needed.
✔ Simulation and Testing of Maintenance Strategies
Manufacturers can utilize digital twin technology to simulate various maintenance strategies within a virtual environment. This allows them to evaluate the impact of different changes without any associated risks, identify best practices, and analyze various scenarios. As a result, these simulations lead to improved decision-making, enhanced operational efficiency, and significant cost savings in maintenance processes.
Why Digital Twins Are the Future of Smart Manufacturing & Maintenance?
For manufacturers, digital twins and predictive maintenance represent a game-changing shift from reactive to proactive operations. By leveraging real-time monitoring, predictive analytics, and simulation-driven decision-making, manufacturers can minimize unplanned downtime, extend equipment lifespan, and optimize resource allocation.
Implementing digital twin technology not only reduces maintenance costs but also improves overall operational efficiency, ensuring a more resilient and agile production environment. With the ability to test and refine maintenance strategies virtually, businesses can make data-driven decisions with confidence, reducing risks and maximizing productivity.
As the manufacturing landscape evolves, companies that embrace digital twin technology will gain a competitive edge, ensuring smoother operations, higher efficiency, and long-term cost savings.
Is your organization ready to take the next step toward smarter manufacturing?
5. Sustainable Production
Sustainable manufacturing is essential for industries aiming to grow economically. It prioritizes environmental responsibility through energy efficiency and waste reduction.
✔ Integration of Renewable Energy Sources
A major trend in sustainable manufacturing is using renewable energy sources like solar and wind power. By adopting these technologies, companies reduce their reliance on fossil fuels. This change helps them manage costs better and protects them from fluctuations in energy prices and regulatory changes, leading to greater energy independence.
✔ Circular Economy Principles
Another major trend is the circular economy, which keeps products and materials in use longer to reduce waste. Manufacturers are creating products that are durable, repairable, and recyclable. They also recycle waste into resources, saving materials and reducing costs while generating new revenue.
✔ Advanced Manufacturing Technologies
Advanced manufacturing technologies, like 3D printing and digital twins, support sustainability. 3D printing reduces material waste by allowing the precise production of complex parts. Digital twins act as virtual models that simulate processes, helping to find ways to save energy and resources. Together, these technologies improve design and efficiency.
2025 and Beyond: Crafting Future-Ready Manufacturing Strategies
The manufacturing sector is poised for significant changes in 2025. Companies must prioritize the adoption of digital technologies to remain competitive. By embracing innovative approaches and advancements, manufacturers can navigate challenges and excel in their industry. Being adaptable and forward-thinking will not only ensure their survival but also position them as leaders in innovation.
Are you looking to enhance efficiency, reduce costs, and improve decision making?
Let’s work together to implement the best technologies to optimize performance and achieve long-term success.