September 27th, 2024
Category: IoT
No Comments
Posted by: Team TA
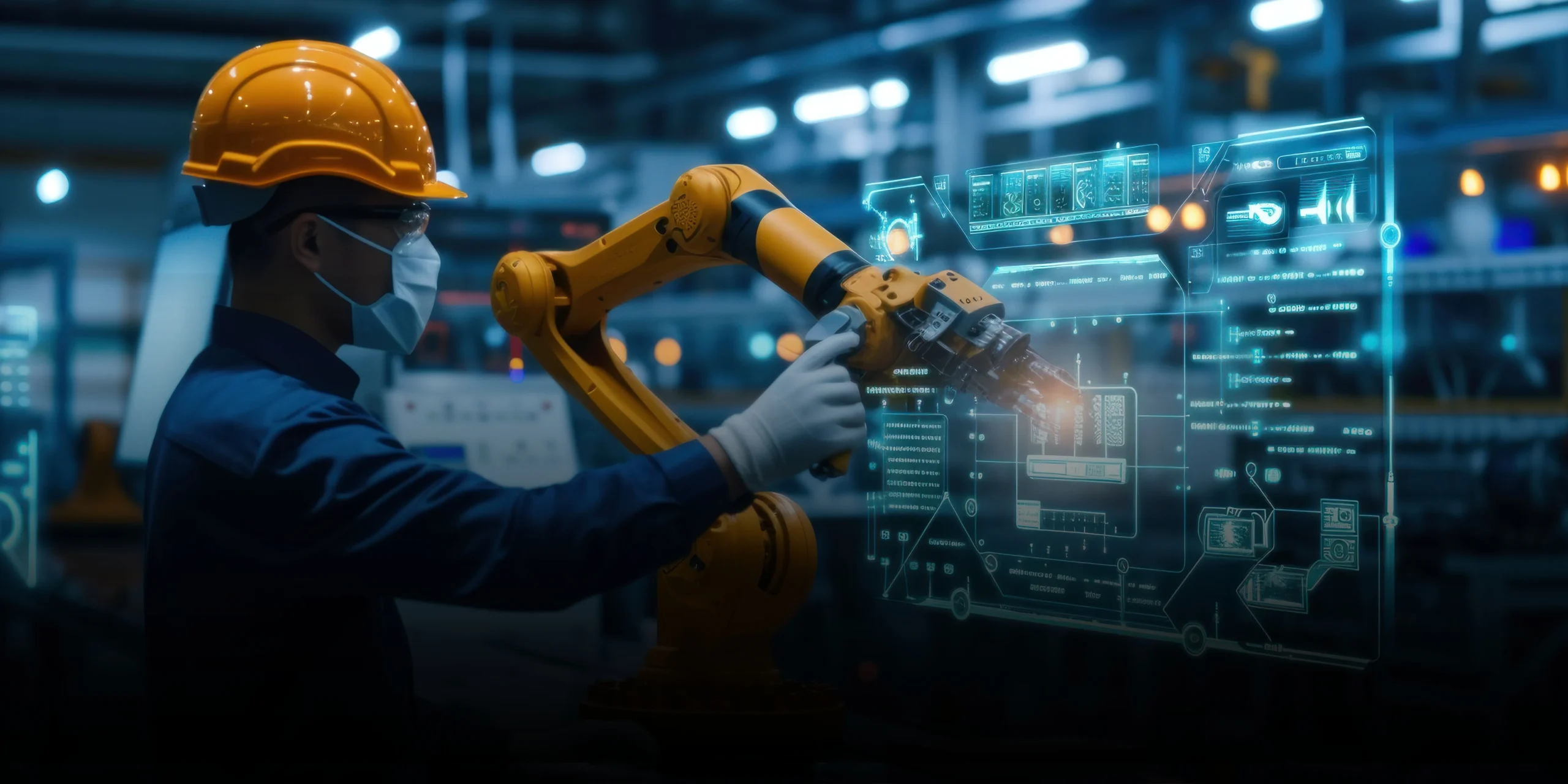
The Internet of Things (IoT) is a network of connected devices and sensors that collect and exchange data, helping manufacturers enhance efficiency and productivity. The industrial IoT is shaping the future of manufacturing by enabling automation through robotics and human-robot collaboration (“cobotics”). It helps predict equipment failures on factory floors and track assets in warehouses, driving efficiency and innovation across manufacturing operations. Fortune Business Insights estimates that the market for IoT in the manufacturing industry was valued at USD 27.8 billion in 2018 and is predicted to reach USD 452.27 billion by 2032 at a CAGR of 22.1%. This blog will explore the applications of IoT in manufacturing industry, highlighting its benefits and upcoming trends to transform the industry.
The Impacts of IoT in Manufacturing Industry
The IoT in manufacturing integrates sensors, smart devices, and network connectivity to enable real-time data sharing between machines and humans. Using artificial intelligence and machine learning (M2M, M2P), IoT-connected industrial robots can reduce unscheduled maintenance and automatically coordinate activities, revolutionizing the industry. According to a McKinsey study, IoT applications in manufacturing could generate an economic impact of $1.2 trillion to $3.7 trillion by 2025.
1. Predictive Maintenance
Many manufacturing companies have faced unplanned downtime, which can be extremely costly. Equipment failures and machine breakdowns can seriously impact production and pose risks to frontline workers, making it a critical issue.
The Internet of Things in manufacturing offers predictive maintenance that leverages data processing and advanced analytics to predict equipment failures before they occur. With IIoT, more data becomes available, improving accuracy in estimating asset runtime. Deloitte reports that predictive maintenance powered by IoT in manufacturing can reduce equipment breakdowns by 70% and cut maintenance costs by 25%.
2. Improved Asset Management
Manufacturers are facing increasing customer demands for faster delivery times. To meet these expectations, they are turning to micro-logistics networks. IoT in connected supply chains helps manage inventory more effectively at the asset level, ensuring quicker, more efficient deliveries.
Today, supply chain leaders are turning to technology to boost efficiency, speed up production and delivery, and automate tasks. IoT plays a vital role, with 55% of manufacturing leaders prioritizing improved supply chain visibility to streamline operations.
3. Boosting Production Efficiency
The Internet of Things (IoT) streamlines production by enabling manufacturers to collect data from machines, identify trends, and monitor real-time production metrics. This allows for improved auditing, quick resolution of issues, and process optimization.
IoT also connects equipment wirelessly, enabling remote control of assets from a central location. Thus, assets can be monitored and controlled remotely which reduces downtime and prevents problems before they occur, boosting overall productivity.
4. Optimizing Quality Control
Earlier quality assurance in manufacturing relied on manual processes that were often prone to errors. Today, IoT technology allows manufacturers to monitor key quality parameters like humidity, temperature, and pressure with greater accuracy.
IoT sensors collect real-time data to identify which products meet quality standards and require closer inspection. This is crucial for manufacturers adhering to strict standards like ISO and GMP, ensuring better process reliability and product quality.
5. Improved Safety
A study published in Safety Science revealed that IoT-based safety monitoring systems reduced workplace accidents by 27% and decreased injury severity by 32% in manufacturing environments. Automation enhances safety by minimizing the risks associated with manual labor and hazardous tasks.
Manufacturing companies are also investing in wearable technology, like IoT-enabled smart glasses and vests, which improve posture during heavy lifting and provide alerts to prevent hazardous behaviors, ensuring safer work conditions.
6. Increased Revenue and Customer Satisfaction Levels
Real-time monitoring of machines allows manufacturers to generate accurate reports and make better, customer-focused decisions. This integration of IoT technology in the manufacturing industry enhances production levels, improves quality, and drives revenue growth for manufacturing businesses.
Remote diagnostics enhance customer satisfaction by reducing repair times and fostering stronger relationships. Early detection drives product quality improvements, leading to better customer satisfaction and increased service value.
Use Cases of IoT in Manufacturing Industry
1. Machine Monitoring to Track OEE/OPE
Industrial IoT enables manufacturers to digitize their analog processes, offering detailed insights into machine performance. By using sensors connected to an IoT gateway, they can monitor machine uptime and unplanned downtime, allowing for accurate tracking of Overall Equipment Efficiency (OEE) and Overall Process Effectiveness (OPE). These metrics serve as valuable benchmarks for driving process improvements and enhancing operational efficiency.
2. Inline Quality Assurance
IoT for the manufacturing industry can improve quality checks by using connected sensors and devices like machine vision cameras, scales, calipers, and temperature and humidity sensors. These smart sensors provide much greater precision than manual inspections. By integrating quality checkpoints throughout the production process, defects can be detected early and resolved before progressing further.
3. Anticipating the Market
Data is essential for evaluating production quality and identifying patterns in manufacturing. It helps manufacturers anticipate necessary changes and make informed decisions, improving inventory management, staffing, and cost control. With IoT technology in the manufacturing industry, predicting and optimizing these needs becomes easier, ultimately leading to better customer satisfaction and streamlined operations.
4. Digital Twins
By leveraging the IoT concept of Digital Twins, businesses can create virtual replicas of physical assets like equipment and spare parts. This enables managers to simulate processes, identify issues, and optimize operations without risking physical damage.
Digital Twins provide real-time insights into inaccessible devices and improve maintenance, as seen with Kaeser, a leading manufacturing company and compressed air products provider which used this technology to shift from selling products to offering services. With the Digital Twin system, Kaeser received operational data on the equipment during its lifecycle, especially the rate of air consumption.
5. Logistics Management
Manufacturing logistics face risks like weather disruptions, fraud, and asset management challenges. IoT connections between devices and systems help tackle these issues by improving warehousing, fleet management, and cargo tracking, driving digital transformation across the supply chain.
For instance, Amazon has improved delivery convenience and reduced costs with drop shipping bots and lockers. Automated order processing, status updates, and connected bots for last-mile delivery help manufacturers lower shipping expenses and enhance customer satisfaction.
IoT Trends in Manufacturing
Machine-to-Machine (M2M) Automation
M2M technology was initially used in manufacturing with SCADA and remote monitoring. This facilitated the transmission of sensor data across networks. This technology enables devices to communicate and make automated decisions, such as materials procurement and sales forecasting, without human input.
Smart sensors play a crucial role in this communication, allowing IoT systems to automate processes effectively. Manufacturers can leverage M2M for tasks like remote monitoring, product restocking, and asset tracking.
To benefit from M2M automation, manufacturers should integrate this data with enterprise software. Connecting ERP systems with products and machines helps technicians monitor performance and gather insights in a unified platform.
IoT Blended with VR and AR
Blending IoT data with VR and AR offers economic benefits, including increased profits, reduced costs, and new opportunities for product innovation. IoT trends in manufacturing are particularly relevant, enhancing AR/VR applications in various ways.
For equipment management, IoT sensors provide real-time data that can be visualized through VR, aiding in the detection of breakdowns. AR helps optimize factory layouts by creating efficient routes and inventory locations. Additionally, VR can be used to simulate equipment operation, offering valuable training for employees based on real IoT data.
Security and Privacy
Privacy and security have become major concerns for IT specialists, especially with the increased visibility of manufacturing systems making them more vulnerable to cyber threats. As factories transition to smart environments, protecting against data leaks, malware, and ransomware is crucial.
To secure the IoT ecosystem, it’s essential to track physical devices to prevent theft, conduct risk assessments, and use encryption. Building awareness and embedding security practices into corporate culture is vital for maintaining a robust and secure IoT environment.
IoT Platforms are Converging and Overtaking Traditional Software
Industrial IoT (IIoT) applications are increasingly integrating with traditional software like ERP, MRP, MES, and finance systems, using collected data to enhance decision-making. They offer asset management, real-time monitoring, and utilization reporting, along with dynamic KPI displays and customized dashboards on the shop floor. As IIoT systems continue to advance, they are likely to become the primary driver of manufacturing operations, potentially making older software redundant.
Key Takeaways
IoT solutions are vital components for modern manufacturing, supporting everything from automation to predictive maintenance. Leading tech companies heavily invest in IoT to drive digital transformation. For example, Microsoft offers Azure IoT Suite, Amazon provides AWS IoT Greengrass, and Google has Cloud IoT Core. These platforms facilitate data collection and analysis, along with tools for continuous mobile monitoring.
To maximize IoT benefits, manufacturers need secure data control and device interoperability. Investing in robust IoT technology enhances system integration, boosts competitive edge, and improves profitability. You can reach out to us, one of the leading IoT companies that offers scalable, secure, and reliable IoT solutions for manufacturers.